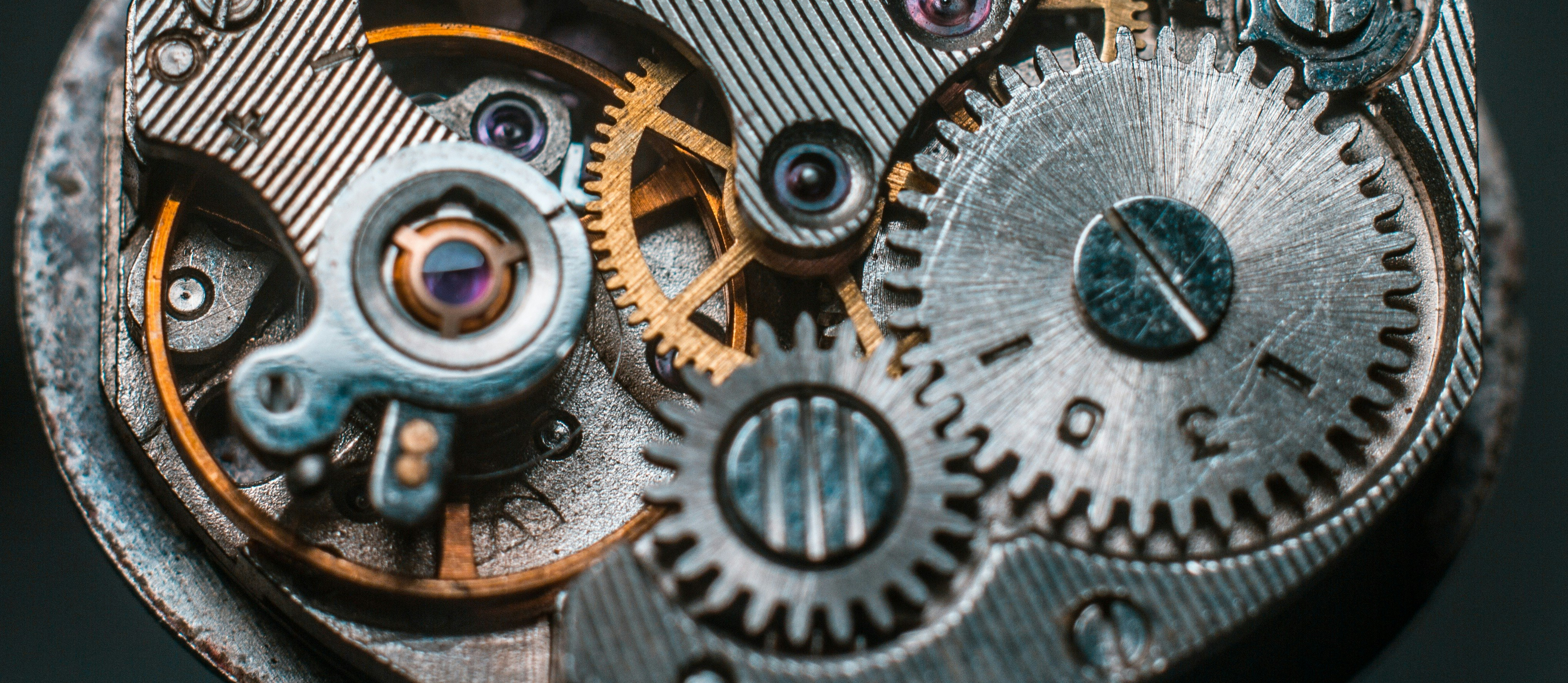
Summary
Skills:
Robotic Arm Project
Developed a planetary gearbox for a 6-axis robotic arm with a base joint actuated by a Nema 17 stepper motor. Calculations revealed that the motor alone lacked sufficient torque (0.41 N*m) to rotate the base. Addressed this limitation by implementing a 5:1 planetary gearbox for increased torque.
Planetary Gearbox
Designed a 3D CAD model using Fusion 360 for the planetary gearbox, featuring a ring gear embedded in the housing, three planet gears with 22 mm bearings, and a sun gear directly connected to the stepper motor's shaft. Achieved an output torque of approximately 2 N*m, exceeding project requirements. Video below shows the assembly of design.
3D Printing Components
Addressed 3D printer error margins affecting gear accuracy by adding a tolerance value to planet gears. Despite the looser fit affecting gearbox performance, it was necessary due to equipment limitations (accuracy of 3D printer.) The video demonstrates the gearbox's output shaft turning, powered by a DRV8825 driver module with a 12V, 1.6 A DC power supply.